Выклеиваем детали из стеклоткани. — Паркфлаер
Друзья. Хочу с вами поделиться как я выклеиваю детали из стеклоткани. И дать несколько советов.Скорее всего я больше судомоделист, чем авиамоделист. Поэтому все фото готовых изделий будут судомодельные. Из стеклоткани можно выклеить впринципе любые детали на вашу модель.
В выклейке деталей есть небольшие хитрости, возможно вы их знаете, но я расскажу о них.
Приготовление правильной эпоксидной смолы. Когда вы приготовили эпоксидную смолу и смешали ее с отвердителем, вы задаетесь вопросом, а засохнет ли она. Она может и не засохнуть так как у нее были не соблюдены пропорции в приготовлении, и чтобы не загубить материалы и труды нужно проверить ее на прочность. Как же это сделать? Нужно капнуть маленькую капельку смолы на фольгу, после этого надо нагреть ее на зажигалке пока эпоксидная смола не закипит. После того, как смола закипела, нужно подождать несколько минут когда она остынет, и попробовать ее. Если она резинистая то ваше изделие тоже будет резинистым( это плохой результат). Нужно чтоб смола была твердая и крепкая! Если вы размешали ее, но после проверки она получилась у вас резинистая, то надо добавить в разведенную смолу немного отвердителя или наоборот смолы. Таким образом каждый раз проверяя мы получим правильную смолу. Я использую вот такую. Смола чаше всего остается эластичной, потому что смола имеет свойство впитывать влагу и перед использованием ее иногда надо прогреть. Также могу порекомендовать харьковскую и Держинскую смолу проблем с ними не было
Подготовка стеклоткани. Перед началом работы нам нужно определить слоистость волокон, а именно чтобы они тянулись в доль.Вначале нам нужно отрезать стеклоткань по размерам детали, которую мы будем выклеивать. Нарезанные куски нам нужно будет отжечь (чтобы парафин, который покрывает стеклоткань, выгорел). Хорошо если у вас окажется строительный фен, которым можно равномерно и качественно обжечь стеклоткань. Но у меня фена нету, и пришлось импровизировать. В подвале я нашел старую советскую электропечь и с ее помощью я смог отжечь стеклоткань от парафина. Зачем нужно отжигать стеклоткань, если без отжига можно выклеить деталь? Стеклоткань нужно отжигать чтобы весь парафин выпарился из нее. И когда мы будем пропитывать стеклоткань эпоксидной смолой она хорошо пропитается и станет намного крепче. Для склейки частей деталей нужна эпоксидная смола гуще. Для этого в готовую смолу подсыпаем и тут же перемешиваем полисорб, пока опоксидка не станет по вязкости как сметана. Если у вас есть готовая матрица, то хорошо ее бы заформовать в вакуумном мешке. Но не у каждого будет компрессор чтоб откачать воздух. Как сделал я. Взял целофановый пакет и с помощью иголок сделал в нем большое число дырочек . После уложения в матрицу стеклоткани взял этот пакет и прикатал к стеклоткани,а ее к матрице. После этого положил параллон на матрицу(чтобы впитал лишнюю эпоксидную смолу), по толщине не больше 15 мм. Я покупал специальный вакумный мешок, который не набирает воздух. После помещения в вакумный мешок нашей матрица, тщательно запаковываем, и с помощью пылесоса откачиваем воздух.
чтобы получилась однородная ( без комочков) мыльная пена, именно ею нужно смазать нашу болванку или матрицу. Желательно делать минимум 3 слоя и после каждого слоя ждать до высыхания(2-3 часа). Не в коем случае НЕЛЬЗЯ использовать жидкое мыло, оно не высыхает, поэтому оно и жидкое. Еще можно использовать как разделительный слот пену для бритья. Таким же мыльным раствором полезно смазать руки пред работой со смолой. После работы руки легко отмываются тёплой водой.
.
Помните, что стеклоткань и эпоксидная смола опасные материалы и при работе с ними нужно соблюдать правила безопасности. Надевать респератор и по возможности перчатки и очки.
Изготовление деталей из стекловолокна и углеволокна в моделизме
Для изготовления крупногабаритных и высоконагруженных частей моделей часто применяются так называемые композиционные материалы, состоящие из «наполнителя» и «связующего». Наполнителем, выполняющим основные силовые функции, обычно является стеклоткань, углеткань ( углеродное волокно) или кевлар (материал из синтетических волокон). В качестве связующего выступают эпоксидные или полиэфирные смолы.
Если для изготовления тонких фюзеляжей радиоуправляемых планеров и многих частей свободнолетающих моделей технология выклейки из композиционных материалов является единственно приемлемой (по соображениям прочности), то в остальных случаях, как правило, есть возможность выбора между композитной и бальзовой конструкцией. Если предстоит разовая работа, то, наверное, стоит отдать предпочтение дереву. Тогда общие трудозатраты и вес модели получаться меньше. В случае же «мелкосерийного производства» лучше овладеть техникой работы с композитом.
Сегодня мы познакомимся с основными приемами выполнения деталей для авиамоделей из композиционных материалов. Сразу отметим, что предлагаемый материал предназначен тем, кто только знакомится с новой для них технологией. Поэтому статья основана на описании упрощенных методик, распространенных среди моделистов «средней руки». При более же профессиональной работе выбор исходных материалов и способы работы с ними настолько специфичны, что в каждом конкретном случае требуют отдельных описаний.
Вначале несколько слов о «сырье». Поскольку тонкостенные детали нередко воспринимают значительные нагрузки, для предотвращения растрескивания связующего в смолы добавляют пластификатор (или при возможности используют специализированные, высокопрочные и не слишком «стеклотвердые») смолы. Чтобы эпоксидку было легче наносить, ее разбавляют растворителем, спиртом или ацетоном. Для тонирования детали можно добавить в смесь типографскую краску или алюминиевую пудру. Неплохие результаты дает и вмешивание в «сырую» смолу художественных масляных красок. Кроме пигментирования, такая краска еще и немного пластифицирует исходную смолу. Стеклоткань, как правило, приходится прокаливать над электрической плиткой или в электродуховке для удаления парафина, которым она пропитывается на заводе.
Прежде всего отметим, что все работы с эпоксидными (да и полиэфирными) смолами нужно проводить в резиновых перчатках в помещении с хорошей вентиляцией. Выклеивание композитных «корок» можно осуществлять как снаружи на болванке, так и внутри, на снятой с нее вогнутой форме (матрице). Болванку можно изготовить из липы, ольхи, плотного пенопласта или бальзы. Ее размеры должны быть меньше размеров детали на толщину будущей «корки». Поверхность следует тщательно зашкурить и загрунтовать.
Затем на матрицу наносится разделительный слой (парафин или полироль для мебели). Стеклоткань нарезается на полосы, которыми можно было бы оклеить болванку без образования складок и «прилачивается» жидкой эпоксидкой. Количество слоев стеклоткани в различных местах детали может варьироваться в зависимости от распределения нагрузок. В случае образования пузырей и вздутий их необходимо сразу же разгладить или прорезать и выдавить из них воздух.
После отверждения смолы «корку» снимают. Если форма матрицы не позволяет этого сделать, деталь разрезают по оси симметрии. При этом, как правило, страдает покрытие болванки, которая будет нуждаться в шпаклевке перед дальнейшим использованием. Недостаток этого способа заключается также в том, что поверхность детали имеет фактуру ткани и требует шпаклевания и вышкуривания.
Для выклеивания деталей по второму способу (матричному) нужно прежде всего изготовить саму «негативную» форму. Обычно она представляет собою толстостенную «скорлупу», выклеенную из стеклоткани.
Если требования к точности детали очень высоки (например, силовые панели обшивки крыла с ламинарным профилем), то матрицу делают в виде массивного «монолита» из гипса, цементного раствора или цемента, смешанного с эпоксидной смолой.
Эталонная модель-болванка должна иметь размеры, совпадающие с внешними обводами детали. Чем лучше будет качество ее поверхности, тем меньше потребуется отделочных работ для каждого изделия в дальнейшем. Обычно методом лакировки с промежуточным полированием стараются довести поверхность до зеркального блеска, чтобы готовые, отформованные в этой матрице детали нуждались только в окраске. В случае же применения тонированной смолы поверхности оказываются полностью готовыми. При изготовлении модели-копии можно воспроизвести имитацию заклепок и расшивки на матрице или еще на эталонной модель-болванке.
Для выклейки матрицы нужно вырезать из толстой фанеры рамку по форме осевого сечения болванки. Надев рамку на болванку, закрепите ее пластилином таким образом, чтобы одна из поверхностей рамки совпадала с плоскостью симметрии болванки. По линии сопряжения выполните из пластилина радиус скругления, равный примерно 2 мм.
Если планируется изготовить монолитную матрицу, на рамку нужно наложить окантовку из досок, имеющих высоту, большую чем половина ширины болванки. На болванку и соответствующие поверхности рамки наносится разделительный слой.
Через несколько часов его нужно натереть до блеска шерстяной тканью. Затем болванка вместе с рамкой оклеиваются стеклотканью. В местах резких прегибов укладывается стекловолокно, пропитанное эпоксидной смолой (его можно получить, разобрав рогожную стеклоткань).
Первый отформованный слой выполняется из стеклоткани толщиной 0,03 мм, затем применяется ткань толщиной 0,2-0,3 мм.
Если же требуется изготовить простую легкую матрицу, а не «монолит», то теперь останется положить лишь несколько усиливающих слоев рогожной стеклоткани. Здесь опять особое внимание нужно обратить на отсутствие пузырей, чтобы дефекты поверхности не передались будущим изделиям.
Для ликвидации пузырей оснастку можно поместить в воздухонепроницаемый мешок (предварительно уложив на нее полиэтиленовую пленку) и откачать из него воздух с помощью вакуумного насоса. Под разряжением форму надо держать до полного отверждения «корки». Если вакуумный мешок не имеет проколов, то для этого достаточно пережать шланг, отключить насос и оставить в таком виде оснастку на 12 часов. В случае изготовления монолитной матрицы всю опалубку заливают гипсовым раствором или эпоксидной смолой с наполнителем (в качестве последнего могут использоваться любые порошкообразные или зернообразные материалы.
После отверждения смолы, болванка с рамкой аккуратно отделяются от полученной формы. Аналогично изготавливается и вторая, симметричная часть матрицы.
При выклеивании корок в полученной матрице применяются те же приемы, что и при ее изготовлении. Первый слой стеклоткани должен иметь толщину 0,02-0,03 мм,
последующие — порядка 0,2 мм. После отверждения смолы «корку» обрезают вровень с краем матрицы, вклеивают шпангоуты (если необходимо) и затем вынимают ее.
Для снижения массы детали часто используют армирование пористым пенопластом, бальзой или слоеные (сендвичевые) конструкции, имеющие дополнительное внутреннее покрытие из тонкой стеклоткани. В этом случае наружное покрытие может быть выполнено из одного слоя стеклоткани толщиной 0,2-0,3 мм. Пенопласт или бальзу нарезают на фрагменты, которым можно было бы придать кривизну пуансона. Пенопласт несложно изогнуть над электроплиткой, а бальзу проще намочить и примотать резиной к болванке до высыхания. Стеклоткань можно пропитывать эпоксидной смолой как в самой форме, так и до размещения в матрице, на какой-либо ровной поверхности (излишки клея снимаются шпателем). Однако пропитанная ткань, особенно тонкая, при укладке имеет тенденцию больше прилипать к перчаткам, чем к пенопласту. Поэтому иногда проще уложить в вакуумный мешок сборку без внутреннего слоя стеклоткани, и «прилачить» его потом. Армирование бальзой имеет то преимущество, что она почти не впитывает в себя связующее.
При склейке между собой тонкостенных корок часто используются промежуточные шпангоуты. В случае же армирования в этом нет необходимости. Эпоксидная смола имеет плохую адгезию к отвержденному стеклопластику. Поэтому соединяемые поверхности нужно зашкуривать крупной наждачной бумагой, а линии стыка оклеивать полосками тонкой стеклоткани. Изнутри на одну из «корок» полезно наклеить отбортовку, которая позволит упростить и увеличить надежность соединения деталей. До момента полного отверждения смолы изделие обматывается скотчем.
При мелкосерийной постройке моделей-копий применяются также различные «гибридные» технологии. Например, внешний слой детали формуется из АВС-пластика и образует внешнюю фактуру поверхности. Далее располагается промежуточный слой тонкого пенопласта. Внутреннее, силовое «покрытие» делается из стеклоткани.
По материалам журнала «Моделизм спорт — хобби»
А. Перфильев
Среди авиамоделистов также популярно изготовление воздушных винтов из композитных материалов применением пресс форм.
Стекловолокно + эпоксидка. Изготовление лицевых панелей любой формы из стеклопластика
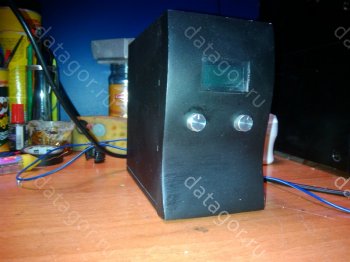
Приветствую жителей и гостей Датагории. Хочу поделиться своим опытом изготовления лицевых панелей из стеклопластика, в данном случае для лабораторного блока питания. Любой панели, для начала, требуется предмет-форма. Так как будущий блок будет из корпуса ATX, скручиваем форму из тех же блоков при помощи саморезов по металлу по размеру будущей панели, а внутри обклеиваем малярным скотчем. Для того чтобы форма не рассыпалась, когда будем доставать, закладываем стекловолоконную шкурку (используется для затирки шпаклёвки у маляров).
Думаю не все читатели данной статьи «заядлые» строители, так что опишу подробно. Для формы можно использовать любую гипсовую штукатурку. Не рекомендую чистый гипс или алебастр, т.к. он очень быстро застывает.
Раствор замешиваем в пропорции одна часть воды плюс три части гипсовой смеси до однородной массы. Аккуратно выкладываем в форму шпателем и разглаживаем до получения нужного вида будущей панели и даём высохнуть примерно сутки. Получается такая конструкция.
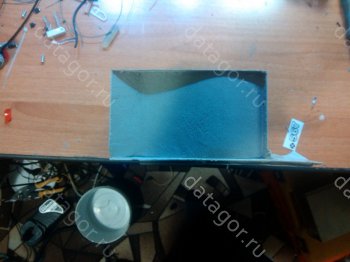
Когда всё застыло, достаём из формы нашу заготовку, на неровности и сколы не обращаем внимания. Обклеиваем малярным скотчем и получаем что-то вроде этого:
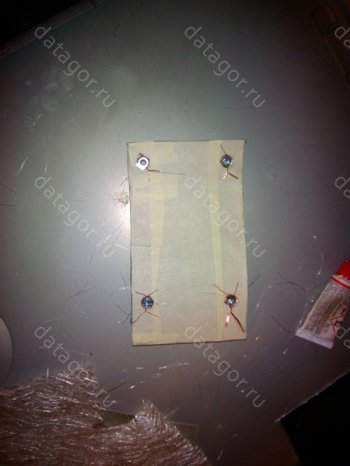
Четыре отверстия по краям, как на фото, не пригодятся, их пропускаем.
Далее — сам процесс. Берём вот такой ремкомплект: стекловолокно, эпоксидка и затвердитель, что продаётся почти в любом авто-магазине.
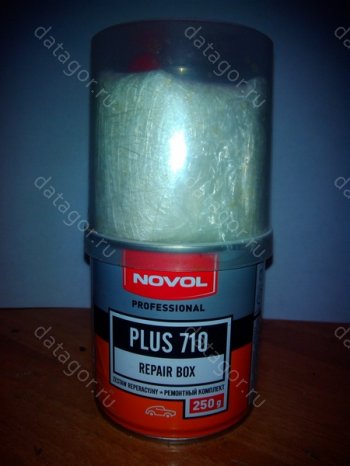
Не забываем о технике безопасности: работаем в перчатках, помещение должно хорошо проветриваться (вонь ужасная), готовая смесь смолы с затвердителем нагревается.
Вырезаем заранее стекловолокно чуть больше по размеру, чем наша предмет-форма.
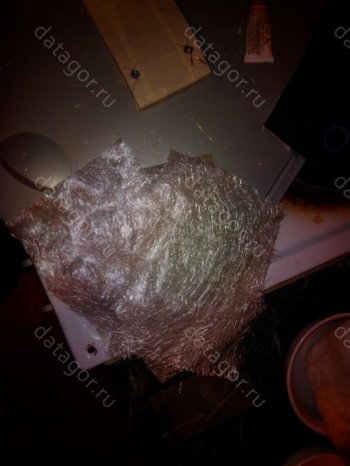
Размешиваем эпоксидку и затвердитель 1:10. Советую замешивать понемногу, быстро сохнет. Итак, раствор замешан. Наливаем на форму и размазываем по всей площади, стараясь не залить края.
Я использовал узкий резиновый шпатель для затирания швов кафельной плитки. Укладываем последовательно все три слоя стекловолокна, аккуратно прижимаем тем же шпателем к форме, сухие места проливаем и разглаживаем. Одного замеса должно хватить.
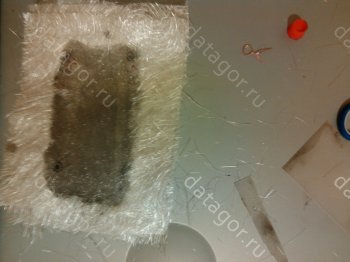
Дожидаемся полной полимеризации эпоксидки, вставляем вверх ногами в ту форму, в которой мы и приготовили нашу предмет-форму и подрезаем «заподлицо» выглядывающее стекловолокно.
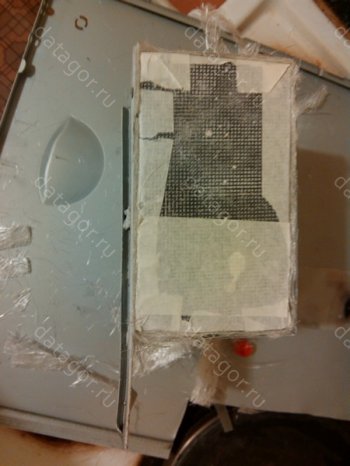
Снова замешиваем эпоксидку и в прямом смысле слова проливаем края, ждём до полного высыхания, сутки не меньше. Получается вот такая заготовка:
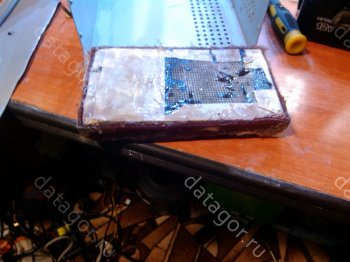
Следующий шаг — грубая обработка. Я использовал «болгаргу» с точильным кругом.

Теперь нужно вытащить вандальским (по-другому не получилось) методом предмет-форму.
Приступаем к выравниванию. Шпаклёвку я использовал универсальную, т.е. по пластмассе и металлу. Замешивается она также как и эпоксидный клей, 1:10.
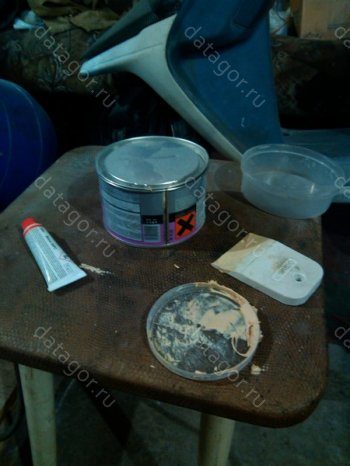
Шпаклюется всё в несколько слоёв, каждому надо давать высохнуть. Перед каждым последующим слоем шкурим, но без фанатизма.
Пришло время окна под дисплей. Вырезаем аккуратно и вставляем оргстекло, по размеру чуть больше, чем используемый дисплей. Шпаклюем.
С нетерпением дожидаемся высыхания шпаклёвки, берём мелкую шкурку (зернистость 500-1000) и доводим нашу панель, насколько это возможно, до идеала.
Для ускорения процесса я использовал шлифовальную насадку на «болгарку».
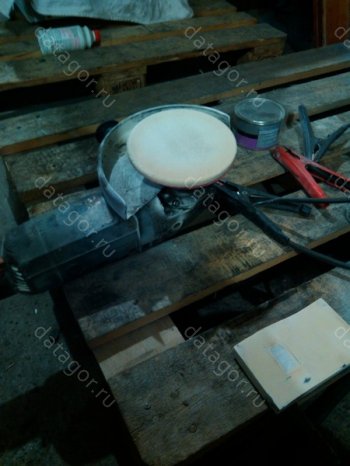
Получилось, по-моему, не плохо.
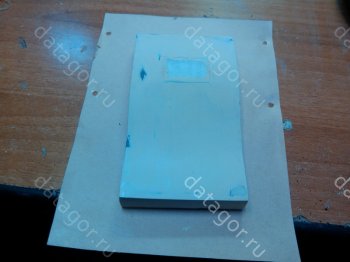
Покраска производится в 5-7 слоёв, иначе будут потёки. Красил обычным баллончиком. Не забываем окно дисплея залепить малярным скотчем.
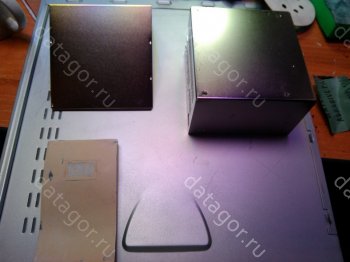
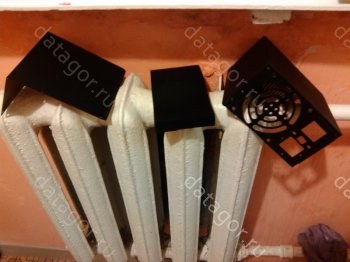
Крепления панели к корпусу блока, без всяких ухищрений прилепил той же эпоксидкой, получилось надёжно.
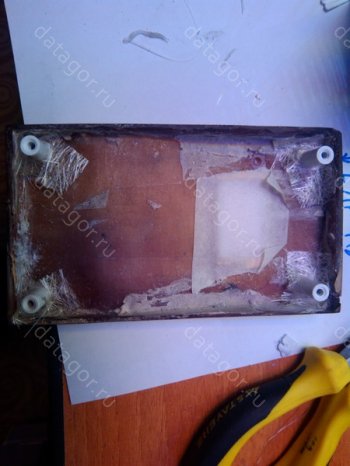
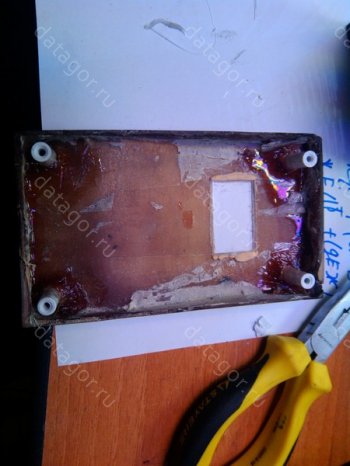
Схему блока питания разбирать не буду. Кому интересно, вот тут подробно «Переделка компьютерного блока питания под зарядное устройство в подробностях»
Крепим все узлы.
И вот что получаем в итоге.
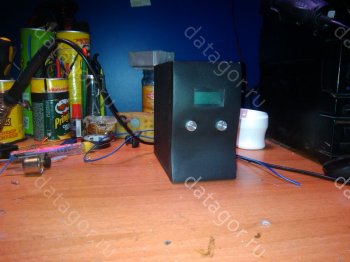
Благодарю за внимание!
Камрад, смотри полезняхи!
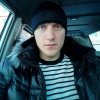
Антон (dedtocha)
Анадырь
О себе автор ничего не сообщил.
Строим корпус из Стекловолокна! Учебное пособие в картинках!
Сообщение от diMIDroll Давай ещё…Очень интерено…по первой аффто: Сабы на чем крепятся? Саморез? Почему гайки закладные не забили заранее…?
Брусочки крепления колец не стали вынимать, как ты упоминал, да?
Ещё интересно что за ткань использовали? Края довольно ровно порезали? чем?
Просто я новые ножницы об 120ую тткань за один пресест убил, очень тупяться…
Мат 9 мм это ДЕВЯТИСОТЫЙ? Как его изнутри клеите? заранее пропитываете? или как и снаружи, положил-пропитал?
Режим ножницами совковыми, специально у портных покупали и под кожу — винил, и для остальных тканей! Ещё есть электрорезак Бош, но не для таких работ!
Клеим по стандартной технологии, намазал, приложил, пропитал, валиком прикатал!
Бруски вынимаем, но не все….
mebius3912Стекломат и изнутри и снаружи, по всем углам плотно, получается очень прочная непродавливаемая корка из стекловолокна! Джипом наезжали на корпус в плоскость, всё ок)
———- Post added 02.01.2011 at 11:35 ———-
Ещё один корпус и почти таже технология, только изначально используем карпет!
Первая примерка компонетов! Каркас корпуса.
Корпус! Чистый обьём 75 литров, порт 125 мм( недоэкспо) настройка 38 гц..
———- Post added 02.01.2011 at 11:36 ———-
ак как вэтом корпусе не так много разнонаправленных плоскостей, для изготовления передней стенки использовали плотный карпет( а не лайкру), после пропитки полиэфирной смолой получается жёсткая конструкция, которую легко проклеивать стекломатом изнутри!
Пропитываем полиэфирной смолой!
Продолжение следует…
———- Post added 02.01.2011 at 11:37 ———-
После того, как пропитанный полиэфиркой карпет застыл, пришло время усилить стекломатом основание динамиков!
Для удобства работы задняя стека корпуса была откручена….
Три слоя 900 го стекломата высохли, прикручиваем заднюю стенку, и усиливаем все углы полосками стекломата, нижний самый острый угол заливаем полиэфиркой и ставим корпус под наклоном! Угла нет!
———- Post added 02.01.2011 at 11:38 ———-
олностью высохший корпус зашкуриваем шлифмашинкой для нанесения финишного слоя шпатлёвки!
Так выглядит зашкуренный карпет полсе пропитки полиэфирной смолой!
Наносим шпатлёвку!
Примерка компонентов!
———- Post added 02.01.2011 at 11:40 ———-
янем, потянем….( материал акустический карпет, ковёр 2.5 мм толщиной, светло серого цвета)