Изготавливаем стекла для фар своими руками
Итак, я получил линзы и решил заняться фарами. Одно из стекол было насквозь пробито камнем, ну и вместо того, чтобы из-за одного разбитого стекла заказывать комплект фар в сборе, было решено изготовить новые стекла из акрилового стекла методом термоформовки своими руками.
Итак, процедура термовакуумной формовки в принципе не сложная:
1. Снимаем стекло.
2. Снимаем матрицу со стекла.
3. Термоформовка акрилового стекла (сплошного поликарбоната) по матрице.
4. Окончательная обработка и подготовка к эксплуатации.
Естественно эта процедура применима к изготовлению любого пластикового изделия, не только стекол фар. А теперь поподробнее о том, как я это делал, с помощью чего и что в итоге получилось… Сразу оговорюсь, что фотографии есть не всех процессов, но самое главное есть!
Первое стекло, за которое не стыдно, у меня получилось только раза с 6-го, хотя второе (на вторую фару) я сделал уже с 1-го, так что не буду описывать все ошибки, а сразу буду писать, что делал с учетом всех подводных камней.
Разбираем фару и снимаем стекло, действия зависят от того, как стекло крепится к фаре — иногда достаточно просто отстегнуть клипсы, но в большинстве своем стекла сидят на герметике и фару необходимо нагреть, чтобы герметик стал вязким, и можно было снять стекло.
Затем с существующего стекла нужно снять матрицу. Есть куча материалов, из чего можно делать слепки, я предпочел строительный гипс. Моем стекло изнутри и заливаем гипсом:
После того, как гипс полностью высохнет (проверяется постукиванием по гипсу — когда высох, он начинает звенеть как камень), вышкуриваем плоскость, пока не доходим до самого стекла:
Ну и выбиваем матрицу из стекла:
Родное стекло фары было 4 мм толщиной, а акриловое стекло под рукой толщиной 2 мм (обычно используют акрил или поликарбонат толщиной 2-3 мм), поэтому следующим этапом стал набор толщины 2 мм, чтобы все зазоры между фарой и прилегающими деталями кузова остались такими же. Набирать можно тоже разными вариантами — я же предпочел 3 слоя стеклоткани.
Укладываем стеклоткань, промазывая каждый слой эпоксидной смолой:
Ну и под вакуум (по поводу вакуумной формовки расскажу позже, когда буду рассказывать про использовании вакуума при декорировании деталей карбоном):
После полного застывания смолы приступаем к шпаклеванию и вышкуриванию. До зеркала выводить не обязательно, главное, чтобы не было выступающих неровностей, т.к. они передадутся на изделие впадиной и сложно будет выводить изнутри до идеального состояния.
Для термоформовки были изготовлены ящик и рамка. Ящик из простого ДСП, все стыки промазаны герметиком, с любого торца отверстие для пылесоса, ну и пластина с кучей дырочек сверху. По периметру проклеен уплотнитель, чтобы рамка плотно прилегала к ящику. Рамка также из ДСП, вернее 2 рамки, между которыми зажимается стекло:
Зажимать стекло в рамке, лучше не снимая защитную плёнку полностью — только периметр, чтобы зажать стекло без защиток. Защитку полностью снимать лучше непосредственно перед нагревом стекла, чтобы было поменьше пыли. При снятии защитки акриловое стекло электризуется и притягивает на себя всю пыль, которая есть рядом…
В целях очистки и диэлектризации акрила используем отличное средство Cosmofen 20. Также им протираем матрицу и размещаем на ящике так, чтобы зазоры со всех сторон были примерно одинаковыми. Под матрицу желательно подложить несколько сантиметровую прокладку, чтобы края изделия после формовки были максимально ровными:
Помещаем рамку со стеклом в духовку, предварительно нагретую до температуры 180 градусов, и выжидаем примерно 5 минут до полного провиса акрилового стекла (стекло провиснет пузырем без ровных плоскостей), в это время включаем пылесос, достаем рамку и быстро как-бы одеваем сверху на матрицу. Фотографий и видео нет, т.к. в процессе не до этого, но в интернете куча видеороликов на эту тему…
В итоге получаем вот что:
Ждем несколько минут, пока пластик немного остынет, чтобы можно было прикоснуться голыми руками, и выбиваем матрицу из изделия. Главное не передержать, т.к. пластик при остывании дает небольшую усадку и выбить матрицу после остывания будет очень проблематично…
Обрезаем излишки с небольшим запасом и 600-й наждачкой выводим все неровности на внешней и внутренней поверхности:
В принципе можно сразу вышкуривать дальше, понижая зерно до 2000 и, и затем отполировать, но я решил ещё и залачить стекло с обеих сторон. В первую очередь для того, чтобы щетки омывателя фар терли не пластик, а лак…
Эту процедуру сильно расписывать не буду, после экспериментов с разными лаками (каждый эксперимент с аэрозольными лаками вел к потере нескольких дней — полное высыхание, попытка отполировать и снятие лака до пластика), я отложил в сторону всевозможное лаки в аэрозольных балончиках, и задул Штандоксом:
Ну и затем подготовил поверхности 1500-й и 2000-й наждачками к полировке, прошелся 3М-овским Тризактом (3000), и отполировал 3М-овскими же полиролями 74-й и 76-й.
Левая фара только задута лаком, правая уже отполирована (капельки воды — стекло ещё не высохло после мытья):
После этого срезаем все излишки по периметру, которые очень сильно пригодились в процессе работы (за них можно и подержать, и подвесить, ну и в конце концов, когда стекла пару раз падали, маленькие трещинки от падений были только на излишках, и в конце спокойно срезались) и вставляем стекла на место.
На фото они только приставлены, чтобы было видно результат, т.к. фару ещё буду доделывать. Даже не было времени дождаться (или терпения не хватило), пока они полностью высохнут, но результат налицо:
Спасибо за внимание, надеюсь кому-нибудь пригодиться…
Изготовление стекол фар своими руками…
Итак, в этой статье я хочу вам рассказать, как можно сделать самому стекло на фару в домашних условиях. Одно из стекол было насквозь пробито камнем, ну и вместо того, чтобы из-за одного разбитого стекла заказывать комплект фар в сборе, было решено изготовить новые стекла из акрилового стекла методом термоформовки!
Итак, процедура термоформовки (термовакуумной формовки) в принципе не сложная:
1. Снимаем стекло.
2. Снимаем матрицу со стекла.
3. Термоформовка акрилового стекла (сплошного поликарбоната) по матрице.
4. Окончательная обработка и подготовка к эксплуатацаии.
Естественно эта процедура применима к изготовлению любого пластикового изделия, не только стекол фар, а теперь поподробнее о том, как я это делал, с помощью чего и что в итоге получилось… Сразу оговорюсь, что фотографии есть не всех процессов, но самое главное есть!
Первое стекло, за которое не стыдно, у меня получилось только раза с 6-го, хотя второе (на вторую фару) я сделал уже с 1-го, так что не буду описывать все ошибки, а сразу буду писать, что делал с учетом всех подводных каменей.
Разбираем фару и снимаем стекло (действия зависят от того, как стекло крепится к фаре — иногда достаточно просто отстегнуть клипсы, но в большинстве своем стекла сидят на герметике и фару необходимо нагреть, чтобы герметик стал вязким, и можно было снять стекло):
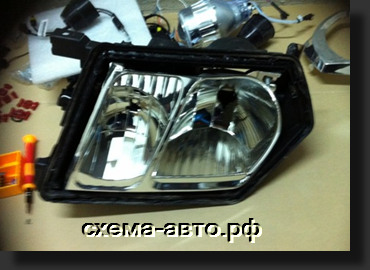
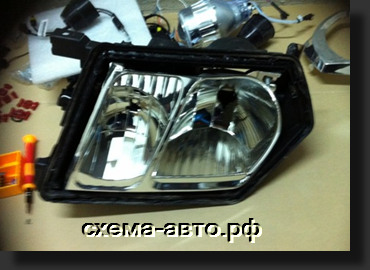
Затем с существующего стекла нужно снять матрицу. Есть куча материалов, из чего можно делать слепки, я предпочел строительный гипс.
Моем стекло изнутри и заливаем гипсом:
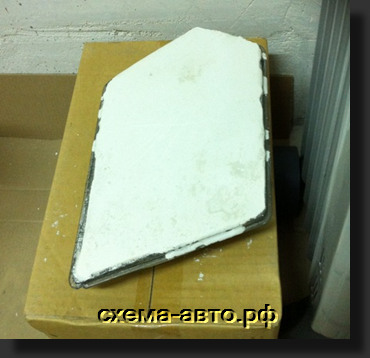
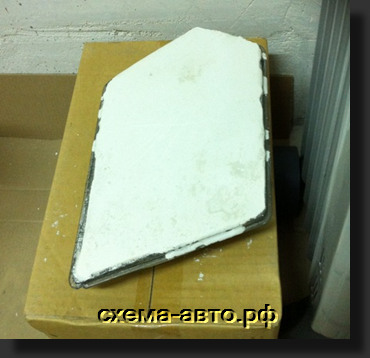
После того, как гипс полностью высохнет (проверяется постукиванием по гипсу — когда высох, он начинает звенеть как камень), вышкуриваем плоскость, пока не доходим до самого стекла:
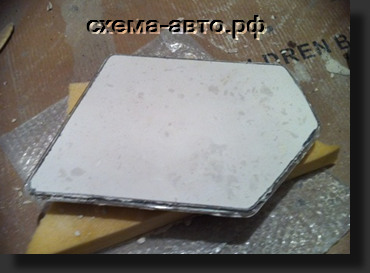
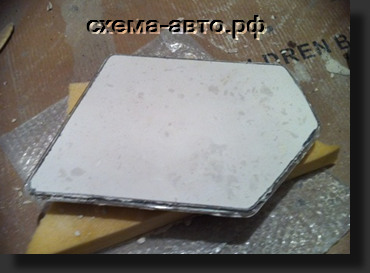
Ну и выбиваем матрицу из стекла:
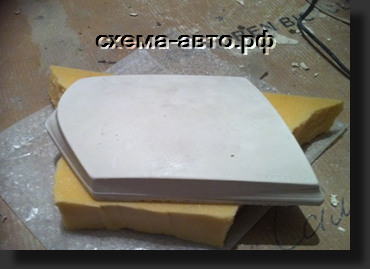
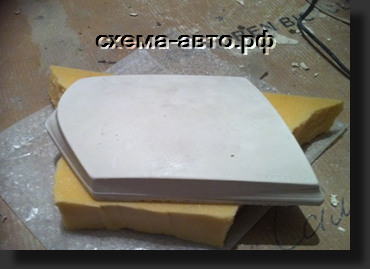
Родное стекло фары было 4мм толщиной, а акриловое стекло под рукой толщиной 2мм (обычно используют акрил или поликарбонат толщиной 2-3мм), поэтому следующим этапом стал набор толщины 2мм, чтобы все зазоры между фарой и прилегающими деталями кузова остались такими же. Набирать можно тоже разными вариантами — я же предпочел 3 слоя стеклоткани.
Укладываем стклоткань, промазывая каждый слой эпоксидной смолой:
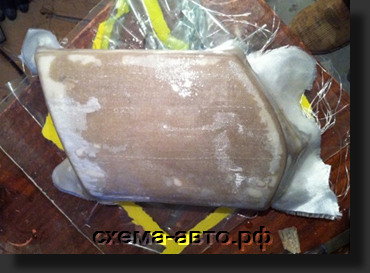
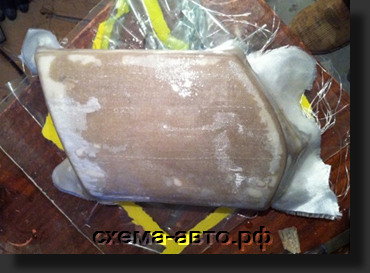
Ну и под вакуум (по поводу вакуумной формовки расскажу позжу, когда буду рассказывать про использовании вакуума при декорировании деталей карбоном):
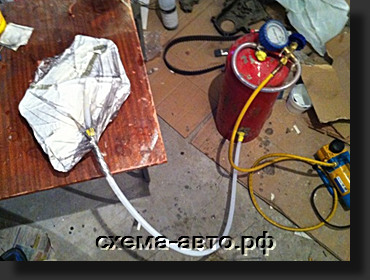
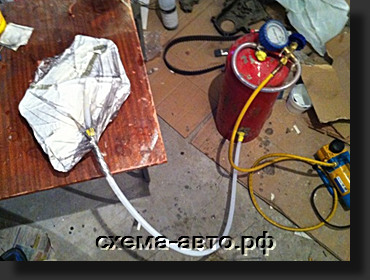
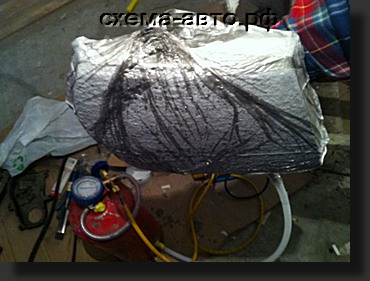
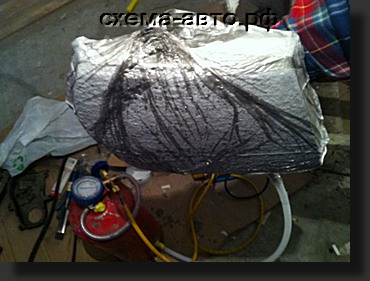
После полного вставания смолы приступаем к шпаклеванию и вышкуриванию. До зеркала выводить не обязательно, главное, чтобы не было выступающих неровностей, т.к. они передадутся на изделие впадиной и сложно будет выводить изнутри до идеального состояния.
Для термоформовки были изготовлены ящик и рамка. Ящик из простого ДСП, все стыки промазаны герметиком, с любого торца отверстие для пылесоса, ну и пластина с кучей дырочек сверху. По периметру проклеен уплотнитель, чтобы рамка плотно прилегала к ящику. Рамка также из ДСП, вернее 2 рамки, между которыми зажимается стекло:
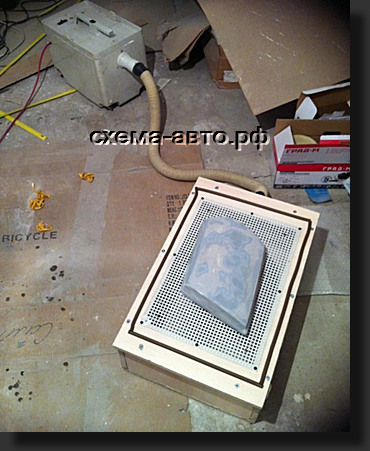
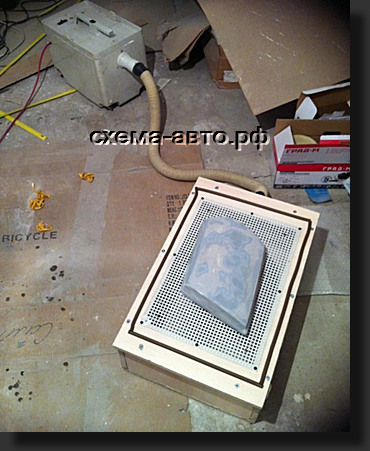


Зажимать стекло в рамке, лучше не снимая защитную пленку полностью — только периметр, чтобы зажать стекло без защиток. Защитку полностью снимать лучше непосредственно перед нагревом стекла, чтобы было поменьше пыли. При снятии защитки акриловое стекло электризуется и притягивает на себя всю пыль, которая есть рядом… В целях очистки и диэлектризации акрила используем отличное средство Cosmofen 20. Также им протираем матрицу и размешаем на ящике так, чтобы зазоры со всех сторон были примерно одинаковыми. Под матрицу желательно подложить несколькосантиметровую прокладку, чтобы края изделия после формовки были максимально ровными:
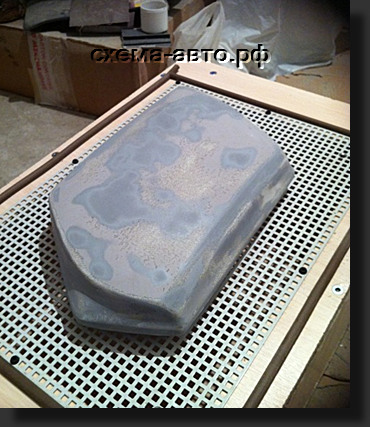
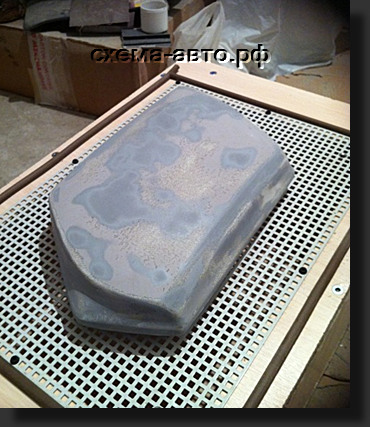
Помещаем рамку со стеклом в духовку, предварительно нагретую до температуры 180 градусов, и выжидаем примерно 5 минут до полного провиса акрилового стекла (стекло провиснет пузырем без ровных плоскостей), в это время включаем пылесос, достаем рамку и быстро как-бы одеваем сверху на матрицу. Фотографий и видео нет, т.к. в процессе не до этого, но в интернете куча видеороликов на эту тему…
В итоге получаем вот что:
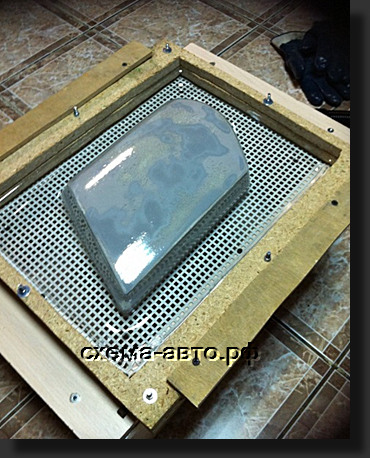
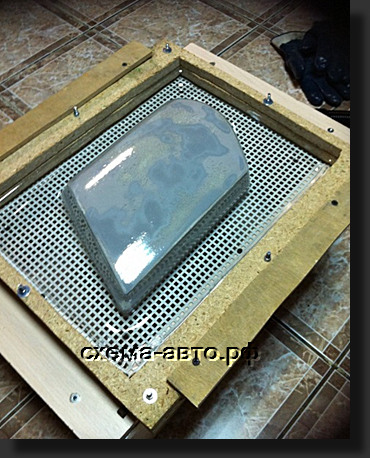
Ждем несколько минут, пока пластик немного остынет, чтобы можно было прикоснуться голыми руками, и выбиваем матрицу из изделия. Главное не передержать, т.к. пластик при остывании дает небольшую усадку и выбить матрицу после остывания будет очень проблематично…
Обрезаем излишки с небольшим запасом и 600-й наждачкой выводим все неровности на внешней и внутренней поверхности:
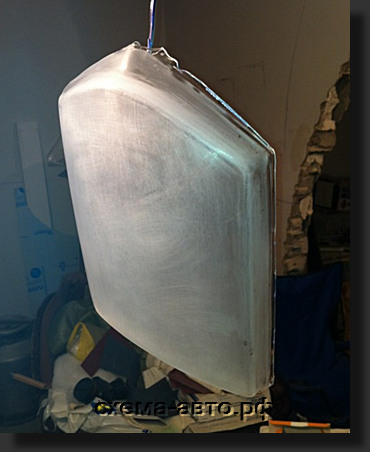
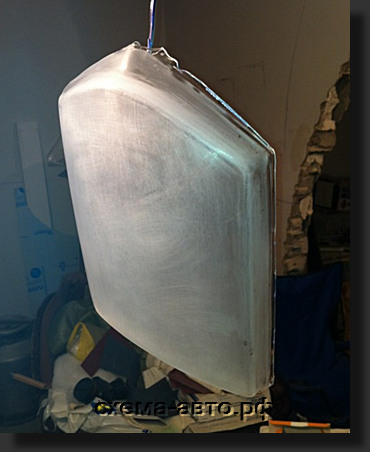
В принципе можно сразу вышкуривать дальше, понижая зерно до 2000 и, и затем отполировать, но я решил ещё и залачить стекло с обеих сторон. В первую очередь для того, чтобы щетки омывателя фар терли не пластик, а лак…
Эту процедуру сильно расписывать не буду, после экспериментов с разными лаками (каждый эксперимент с аэрозольными лаками вел к потере нескольких дней — полное высыхание, попытка отполировать и снятие лака до пластика), я отложил в сторону всевозможное лаки в аэрозольных балончиках, и задул Штандоксом:
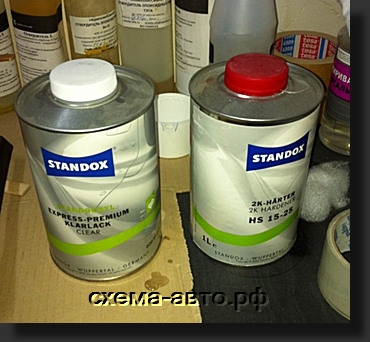
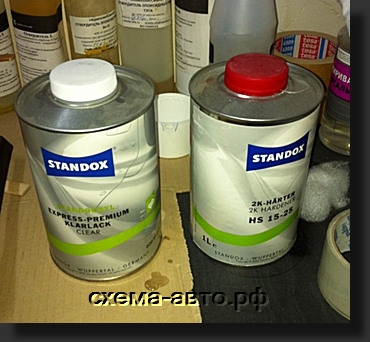
Ну и затем подготовил поверхности 1500-й и 2000-й наждачками к полировке, прошелся 3М-овским Тризактом (3000), и отполировал 3М-овскими же полиролями 74-й и 76-й.
Левая фара только задута лаком, правая уже отполирована (капельки воды — стекло ещё не высохло после мытья):
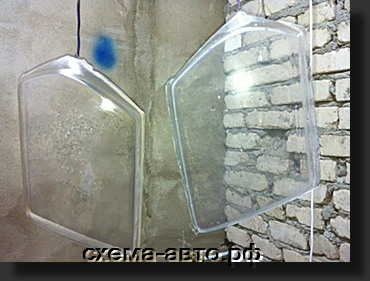
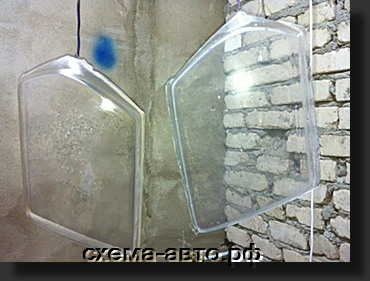
После этого срезаем все излишки по периметру, которые очень сильно пригодились в процессе работы (за них можно и подержать, и подвесить, ну и в конце концов, когда стекла пару раз падали, маленькие трещинки от падений были только на излишках, и в конце спокойно срезались) и вставляем стекла на место.
На фото они только приставлены, чтобы было видно результат, т.к. фару ещё буду доделывать, но об этом позже. Даже не было времени дождаться (или терпения не хватило), пока они полностью высохнут, но результат налицо:
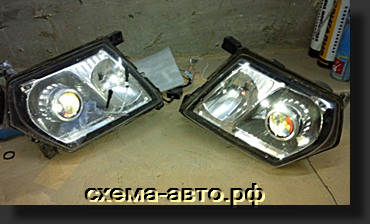
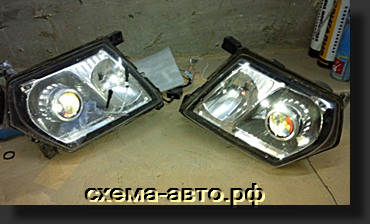
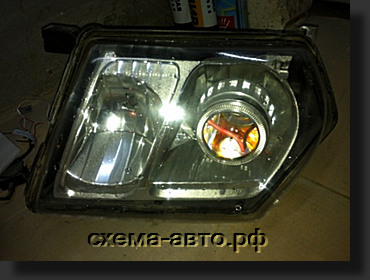
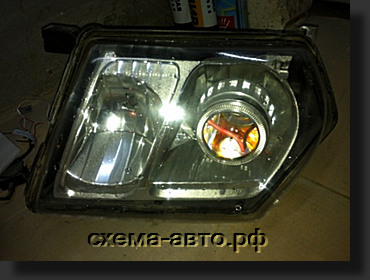
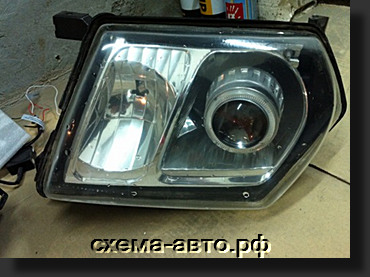
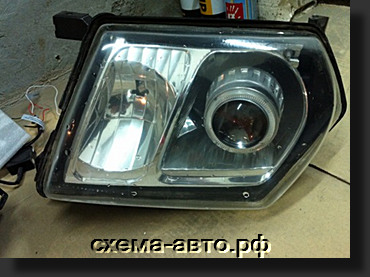
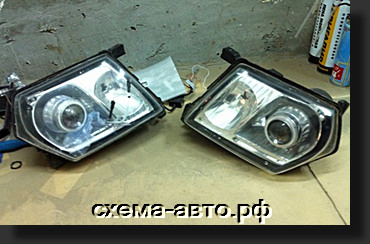
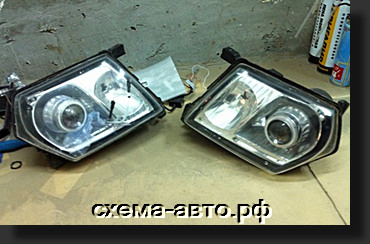
Ну вот вроде и всё, желаю всем удачи…
Автор; Алексей Нуйсков
Изготовление фар из поликарбоната своими руками
Поликарбонат – наиболее востребованный строительный материал, который используется не только для обустройства гражданского и производственного сектора, но и в машиностроении. Ведь уже несколько лет, как промышленность старается минимизировать использование стекла, так как акрил в 200 раз прочнее и безопасней, при этом не уступает в своих функциональных особенностях. Вот поэтому все чаще опытные автолюбители предпочитают фары из полиэфира угольной кислоты. В обзоре мы решили рассказать, как делаются фары из поликарбоната.
Заготовка
Спрос
Изготовление фар из поликарбоната – это превосходный маркетинговый ход, который существенно повышает первоначальную стоимость автомобиля. Одно из самых важных требований, которое предъявляется материалу для изготовления фар – это прочность. Как говорилось выше, поликарбонат в 200 раз прочнее и долговечней. А если вспомнить качество дорожного покрытия, то поликарбонат стает фаворитом.
Процесс производства
Последовательность изготовления
Для изготовления фары из поликарбоната своими руками вам не потребуются дорогостоящие специальные инструменты. Если вы сомневаетесь в своих способностях, то можете обратиться в СТО, там вам индивидуально подберут фары для вашей модели автомобиля. Последовательность проектирования:
- Производимдемонтажиразбираемготовуюфару, вынимаем стекляннуюповерхность. Наданномэтапенедолжновозникнутьсложностей, таккакбольшинстводеталей крепятсянаклипсах. Нобываютслучаи, чтоизделие закрепленогерметиком. Вданномслучаенеобходимохорошоразогреть деталь иотчиститьотслояклея;
- Делаем«болван» илислепок. Изготавливаеманалогичнуюдетальприпомощигипса. Заливаемегоповсемупериметрувогнутойповерхности. Послечегодостаемгипсовый слепок. Теперьприступаемкукладке3-хслоевстеклотканиипромазываемэпоксидной смолой. Готовыйслепокпотребуетсяпоместитьподвакуумдлядальнейшего застывания (длительностьнеменее24часа). Послеокончательногозатвердения снимаемвсенеровностисформы;
- Термическаяобработкаакриладляформированиядеталипослепку. Нагреваемдуховкудо190градусов. Передэтимизготавливаемформуизвосьмиреек, которые закрепленымеждусобойсаморезами. Вполученнойформезажимаемлистиз стеклоткани. Защитнуюпленкунеобходимоснятьпереднепосредственнымнагревом, таккакиз-застатическогоэлектричествамогутпоявитьсякрапленияпылии т.п. Ждем, покаполикарбонатполностьюнепровиснет. Послечегобыстроизвлекаем егоиздуховогошкафаиодеваемнаготовую матрицу. Можнотакжевоспользоватьсявакуумным насосом. Чемменьше паразитныйобъемоткачки — темлучше. Чембольшересивер — темлучше. Герметичностьиспользованнойвакуум-системыдолжнабытьмаксимальнополной;
- Подготовкаиустановкадеталидлядальнейшегоиспользования. В заключительнойстадииизготовленияфары своимируками, вампотребуетсяпроизвестишлифовальныеработы, атакжеустановитьготовоеизделиенаавтомобиль.
Изготовление стекол фар из поликарбоната менее кропотливо как это может показаться на первый взгляд. Длительность изготовления акрила составляет около одного часа, не считая застывания формы под прессом.
Преимущества и недостатки
Автомобильные изделия из поликарбонатного вещества пользуются большим спросом. Многие зарубежные производители изготавливают передние детали машин не твердыми, для чего применяется поликарбонат. Ведь на сегодняшний день есть ряд определенных постановлений о безопасности пешеходов, где сказано, что передняя часть автотранспорта не должна быть изготовлена из твердых материалов.
Помимо всего сказанного можно выделить такие положительные свойства:
- Приналичиисоответствующихинструментовможностекладляфаризполикарбонатасделатьсвоимируками;
- Вслучаеотсутствиянавыковвсфереизготовленияимонтажаполикарбоната, можнообратитьсявавтомастерскую, стоимостьизделиядоступнакаждомуавтолюбителю;
- Стойкиекразличнымвидаммоющихсредств;
- Долговечностьизделиязаключаетсявспециальнойзащитнойпленке, которая непосредственнонаноситсянаполикарбонатноеизделие. Даже, еслисовременемпленкастанетпрофнепригодной, изделиепродолжаетслужитьнеодингод;
- Вслучаеобнаружениямелкихцарапин, срокэксплуатацииможноувеличитьблагодарянаждачнойбумаге, полироли, абразивнойпастыит.п.;
- Высокая ударопрочность. Выдерживаетсильныеударыметаллическимпредметом.
Ряд недостатков фар из поликарбоната:
- Непротивостоитультрафиолетовымлучам. Со временемизделиежелтеетимутнеет, снижаяпроходимостьизлучаемогосвета;
- Неможетпротивостоятьщелочнымвеществам;
- Вмалойстепенимогутрастворятьсявсложныхэфирах, кетонеивароматическомуглеводороде.
Подведем итоги
Автор:
Антон Ермолов
Как сделать фары из поликарбоната
На сегодняшний день поликарбонат представляет собой наиболее ценный и популярный материал, который активно применяется не только при обустройстве производственных и гражданских секторов, но и в современном машиностроение. На протяжении нескольких лет промышленность стремиться свести к минимуму количество потребляемого стекла, заменив его более безопасным и устойчивым акрилом. Именно поэтому все большее количество автомобилистов задумываются над тем как сделать фары из поликарбоната, которые по своим качественным характеристикам значительно превосходят классические стеклянные модели?
Создание фар собственноручно: просто и доступно
Чтобы изготовить собственными силами поликарбонатные фары совершенно не потребуется приобретать особые дорогостоящие инструменты и расходные материалы. Достаточно придерживаться простого алгоритма действий, который и поможет получить отличный результат:
- Выполняем демонтаж и разбор имеющейся фары, вынимая при этом поверхность из стекла. Этот подготовительный этап не должен вызывать каких-либо трудностей, так как большая часть деталей прикреплены по средствам клипс.
- Изготавливаем слепок (“болван”). Делаем по средствам гипса аналогичную деталь. Заливать его требуется в вогнутую поверхность по всему ее периметру. Как только гипс полностью застынет, его нужно аккуратно изъять.
- Далее на гипсовый слепок выполняем прокладку в 3 слоя стеклоткани, листы которой промазываем эпоксидной смолой. Подготовленный слепок помещаем в условия вакуума, чтобы он мог полностью застыть (длительность такого процесса не должна быть менее 24 часов). Как только все затвердеет окончательно, с формы нужно будет ликвидировать даже малейшие неровности.
- Значительно трудоемким и ответственным этапом, который поможет в вопросе о том, как сделать стекло для фары из поликарбоната, станет термическая подготовка акрила, для дальнейшего формирования из него детали по слепку. Духовой шкаф нужно прогреть до 190 градусов. Пока он будет доходить до нужного температурного режима, следует выполнить форму при помощи 8 реек, скрепленных между собой по средствам саморезов. Лист из стеклоткани зажимаем в полученной форме. Перед процедурой нагрева обязательно необходимо снять защитную пленку, так как из-за воздействия статического электричества могут возникнуть крепления частичек пыли. Ждем того момента, когда поликарбонат провиснет полностью.
- После расплавления оперативно достаем материал из духовки и накладываем его на подготовленную матрицу. Также можно использовать вакуумный насос. Чем большим будет ресивер и меньшим паразитный объем откачки, тем лучший получится результат. При этом использованная вакуумная система должна иметь максимально полную герметичность.
- Деталь готовим и монтируем для дальнейшей эксплуатации. На завершающем этапе следует выполнить шлифовальные работы, после чего изделие можно будет устанавливать на автомобиль.
Важно! Процедура создания поликарбонатных фар не является слишком трудоемкой и длительной, как это кажется в самом начале пути. В целом процедура может занимать не более одного часа, если не считать время, которое отводится на затвердевание под прессом формы.
И если кто-то стремится улучшить свое транспортное средство, но не знает, как сделать фары из поликарбоната своими руками, то приведенная выше подробная инструкция поможет выполнить все быстро и максимально правильно. В результате автолюбитель получит отличную оптику, обладающую высокой прочностью, износостойкостью и надежностью.
Желаете построить деревянную теплицу или какое-то другое сооружение из древесины? Тогда узнайте, как делается крепление поликарбоната к дереву, если вы будете следовать нашим советам, то у вас все получиться.
Если вы будете использовать листовой поликарбонат в строительстве, то прочитайте здесь — http://moypolikarbonat.ru/tehnicheskie-harakteristiki-listovogo-polikarbonata-podrobnyiy-razbor/ его подробные технические характеристики.
Читайте также и другой интересный материал:
♦ Рубрика: О материале.Изготовление стекол фар из акрила своими руками
О том что стекло в фаре представляет практически половину, а то и большую часть его ценности говорить не приходится, об этом узнаешь наверняка, когда оно приходит в негодность. О причинах поломки стекла также можно умолчать, так как факторов способствующих тому множество. Не знаешь где найдешь, а где потеряешь…
Процесс изготовление стекол фар из акрила своими руками
Сразу скажем, что процесс изготовления фар будет происходить с использованием материала – акрил. Не поликарбонат, а акрил. Это важно! Теперь начнем. Прежде необходимо снять точную копию стекла фары для изготовления матрицы, по которой будет изготавливаться наш аналог.
Теперь закладываем в стекло художественный гипс, и ждем, пока он затвердеет.
Далее стачиваем гипс со стороны закладки до уровня стекла. Полученную форму извлекаем из старого стекла.
Теперь надо соотнести толщину штатного стекла и толщину акрилового стекла, из которого вы собираетесь изготовить новое. Она должна быть идентична, если нет, то придется компенсировать разницу толщин с помощью матрицы.
Если стекло тоньше штатного, как в нашем случае, то будем наращивать матрицу с помощью стекловолокна, слой за слоем. В нашем случае надо нарастить было 2 мм. Чтобы стекловолокно точно и равномерно облегало форму, его лучше уложить в пакет и высосать воздух.
Вакуум будет равномерно прижимать стекловолокно к гипсу, тем самым обеспечивая точность формы.
После застывания стекловолокна можно приступать к непосредственной формовке акрилового стекла. Для этого нам потребуется приспособление, принцип которого будет основан на всасывании воздуха со стороны заготовки, что позволит создать разность давлений с двух сторон акрила, тем самым обеспечивая прилегание стекла к форме.
Но обо всем по порядку… Приспособление представляет собой ящик с крышкой в виде решетки, а с боку у него имеется отвод на всасывающий пылесос.
Также изготавливается крышка, которая герметично прилегает к ящику и в которую зажимается акрил, подлежащий формовке. Защитную пленку с акрила не снимаем до последнего, то есть до разогрева. Также перед установкой в печь лучше сбрызнуть акрил антистатиком, чтобы не набрать лишней пыли на стекло.
Далее включаем пылесос. Выкладываем матрицу на решетку. Можно выложить ее на чуть большей высоте, чтобы иметь запас под обрезание акрила. Разогреваем акрил. Вот здесь пожалуй самая сложная задача. В зависимости от типа акрила необходимо разогреть его до нужной температуры, при этом он не должен пузыриться, а должен стать пластичным. Лучше вначале поэкспериментировать на маленьком кусочке, а потом уже и на основной заготовке.
В зависимости от типа акрила и толщины рекомендуются следующие температурно-временные режимы. Смотрите таблицу ниже.
литье | экструзия | |
Температура нагрева | ||
Минимальная температура (°С) | 130 | 140 |
Максимальная температура (°С) | 200 | 190 |
Рекомендуемая температура (°С) | 165-190 | 160-175 |
Продолжительность нагрева | ||
Конвекционная печь (мин./мм) | 3-4 | 2,5-3 |
Одностороннее инфракрасное облучение (сек./мм) при интенсивности 2,2 Вт/см² | 42-52 | 38-45 |
Двустороннее инфракрасное облучение (сек./мм) при интенсивности 3,5 Вт/см² | 24-32 | 22-27 |
После того как акрил разогрет, вытаскиваем его из печи и накладываем на матрицу.
Теперь стекло обтянет матрицу, тем самым приняв ее форму. Ждем пока акрил можно трогать руками и снимаем его с матрицы. Не затягиваем с этим, так как остывший акрил может сильно осесть, что создаст трудности в его снятии с матрицы.
Начинаем механическую обработку акрила с помощью болгарки и шли машинки. Края режем в соответствии со стеклом фары, а неровности фары шлифуем.
Акрил материал мягкий и не стойкий к механическим воздействиям. Поэтому его лучше покрыть лаком. Более подробно о такой процедуре в статье «Восстановление прозрачности фар с помощью лака».
Теперь осталось вставить стекло в фару, а фару на машину.
Резюмируя вышеприведенную информацию можно сделать вывод о том, что такой способ будет хорошей альтернативой для тех случаев, когда стекло фары стоит слишком дорого и его не целесообразно покупать, либо его невозможно приобрести вообще. Да, акрил имеет свои недостатки. Такие как наличие опыта работы с ним и низкие механически износостойкие свойства. Тем не менее, соизмерив все «ЗА» и «ПРОТИВ» такой вариант можно назвать вполне жизнеспособным.
Еще хотелось отметить и тот факт, что данную технологию работы с акрилом можно применить не только для изготовления стекол фар, но и для изготовления других корпусных деталей.
Фото предоставлены The-Witcher (г. Уфа).
125 фото уникальные модульные фары для различных автомобилей
Каждый автовладелец понимает, как сложно ехать в плохую погоду. Если регулярно приходится находиться за рулем, делает все, чтобы обезопасить себя различным образом от неприятных моментов на дороге.
Именно по этой причине как сделать фару своими руками – это вопрос, который появляется в запросах поисковиков особенно часто в сезон дождей, снега, поскольку именно установка на машине противотуманных фар дает возможность обеспечить нормальную видимость на дороге.
Содержимое обзора:
Важный атрибут
Основное предназначение противотуманных фар заключается в улучшении видимости ситуации на дороге в случае непогоды, поэтому как делать противотуманные фары должен знать каждый автовладелец.
Их использование значительно повышает показатель безопасности не только пассажиров того автомобиля, в котором они установлены, но и всех остальных участников движения.
В случае плохих погодных условий простые фары обычно совсем бесполезны, поскольку от малейших капель воды световой луч сразу же отражается, как следствие появляется ощущение, словно машина в данный момент времени находится в своеобразном пятне света, мешающем водителю в принципе видеть, куда он направляет транспортное средство.
Благодаря использованию противотуманных моделей фар удается рассеять свет прямо перед машиной, которая движется по трассе. Так получается благодаря тому, что луч выходит достаточно плотный.
Если вы ранее делали регулировку фар, наверняка замечали, что такие фары чаще всего излучают свет желтого/белого света, могут быть установлены как спереди машины, так и соответственно сзади.
На процесс выполнения регулировки влияют условия окружающей среды, но сделать ее достаточно просто без специализированных навыков.
Рекомендуем посмотреть еще тут
Важный момент
В некоторых машинах производители намеренно пытаются сэкономить различным образом на проведённой электрике и часто встречается такая ситуация, когда свет, который в теории должен быть максимально ярким, никак не может чисто технически проявить себя полноценно по причине того, что не получает достаточное количество энергии.
Если говорить о плохих погодных условиях, то вопрос как сделать крепление фар чаще всего появляется в том случае, когда установленные производителем фары элементарно не в состоянии справиться с непогодой в силу маленького числа диодов.
Если у вас есть сомнения относительно целесообразности данной покупки и ее регулировки, то важно иметь в виду, что абсолютно любые противотуманные фары используются не только в случае плохих погодных условий.
Часто автовладельцы говорят о том, что применение такого света защищает от возможного дорожно-транспортного происшествия при условии, что на дороге большое число поворотов, поскольку свет просто стелется по асфальту, а не бьет прямо в глаза.
На что обратить внимание при покупке фар?
Во-первых, если вы решили узнать, как сделать светодиодные фары самостоятельно, то внимательно в магазине посмотрите на то, насколько прочный у фар корпус и, какая толщина стекла.
Во-вторых, посмотрите, есть ли возможность выполнения ремонта одной из составляющих фар, например, стекла.
Рекомендуем посмотреть еще тут
В-третьих, необходимо оценить аэродинамичность и качество крепления.
Нужна ли помощь профессионала
Прежде чем узнавать, как сделать задние фары следует проанализировать, что будет выгоднее: обратиться за оказанием услуг к профессионалам или же выполнить самостоятельную установку фар.
Как установка, так и последующая регулировка фар самостоятельно вполне реальна. Даже не нужно иметь каких-либо специальных профессиональных навыков.
Кроме того, этот процесс не займет много времени. Многие автовладельцы даже отмечают тот факт, что выполнив однажды самостоятельную установку, потом можно легко обучить этому делу своего знакомого.
Что понадобится для самостоятельной установки/регулировки
- Автомобильные фары;
- Провода, необходимые для подключения. На практике они часто уже есть в комплекте;
- Инструмент для осуществления врезки оптики аккуратно в бампер и для выполнения установки светового оборудования.
Набор минимальный и стоит отдельно выделить лишь на реле. Каким образом оно устанавливается подскажут специально оборудованные места для таких осветителей.
Рекомендуем посмотреть еще тут
Также облегчит процесс установки дополнительная кнопка, ответственная за включение фар в салоне автомобиля.
Фото советы как сделать фары
Вам понравилась статья? Поделитесь 😉
Всего посмотрели 180
посетителей. Рубрика:Изготовление плафонов для фар | Хроники Фрилансера — ТавроБлог
Установка линзованной оптики в ТавроФары, да и вообще в фары, имеющие стеклянные колпаки иногда затруднена изза ребер, которые нанесены на рассеиватель. ЧТобы их зашлифовать надо приложить немалые усилия, стекла хрупкие, бъются, то есть процесс еще и достаточно дорогой.
Однако, оказывается, можно пойти и другим путем, — то есть сделать фары на основе прозрачного карболита или оргстекла.
Часть 1. Создание матрицы
План был такой — по форме стекла фары и поворотника делается прозрачный колпак. Так как через него будут светить готовые модули, в т.ч. «линзованые», оно должно быть прозрачным и без рисунка. Поэтому «родное» стекло не годится.
Шлифовать внутренности автор не стал, из-за его тонкости и крайней непрочности. Одно и без шлифовки лопнуло прямо в руках.
Поэтому при помощи шурупов и пены из стекла от родной фары (и поворотника) был слеплен шаблон, на куске фанеры.
Затем его поверхность была зашпаклевана и получилась болванка.
Затем по этому болвану начал выклевать матрицу для вакуум-формовки стекла. Процесс обычный эпоксидная смола + стеклоткань.
Для того, чтобы получить точную форму и избежать пузырьков, засунул болван с налепленой стеклотканью и смолой ( пока она еще жидкая) в мешок для мусора и пылесосом откачал из него воздух. Процесс показан на второй фотке. Виден черный мешок для строительного мусора с болванкой внутри и шланг от пылесоса. Откачивал 10-15 мин на минимальной мощности. Как только смола затвердеет пылесос можно отключить.
Когда эпоксидка засохла получил «слепок» формы будущего стекла. Он еще тонкий и его предстоит усилить несколькими слоями стеклоткани и эпоксидки. (на третьей фоте)
Цель такая: получить «корыто», внутренняя поверхность, которого будет — наружной поверхностью готового стекла. Затем в нижней точке матрицы делается тонкое отверстие через которое насосом будет откачиваться воздух. А разогретый пластик будет втягиваться внутрь корыта.
Сами фары планируволось крепить на металлические кронштейны приблизительно такой конфигурации как на фотографии проекта.
Таким образом, для изготовления фары предстоит сделать две детали: собственно несущий кронштейн и стекло.
Часть2. Окончательная обработка матрицы.
Закончена выклейку матриц для формовки стекла. Для этого полученные ранее «слепки» закрепил термоклеем на кусках
изогнутого гофрокартона. После этого наклеено еще 6 слоев стеклоткани 300-450 г/м2.
В конце необходимо получить нечто вроде тарелки, чашка которой в точности повторяет наружную геометрию фары и поворотника а ее бортики должны быть максимально приближенными к плоскости (идеал) или хотя бы к цилиндрической поверхности.
Последнее, необходимо для того, чтобы разогретый пластик можно было достаточно просто прижать к форме.
На следующем фото можно увидеть полученную деталь. В данном случае это матрица для формовки левой фары. В дальнейшем картонка будет удалена, так как рабочая поверхность матрицы сейчас находится внутри конструкции. Такой изгиб плоскости отбортовки матрицы потребовался для того, чтобы уменьшить вытяжку пластика при формовке.
Матрица для формирования стеклаМатрица для формирования стеклаМатрица для формирования стеклаПервоначально планировалось использовать 5мм материал, но в итоге все делалось из 2мм поликарбоната, стоимость которого 120 грн/метр с доставкой из Запорожья в Киев. Из этого квадратного метра получается 4 стекла («Опель» «Астра»). Себестоимость одного = 120 + 30 = 150 грн.
часть 3
После выклейки матрицы удаляем технологический картон, шкурим, шпатлюем несколько раз для получения ровной, гладкой без сколов и т.п. поверхности. Остается вклеить патрубки для подключения вакуум-насоса и заняться формовкой.
Почти готовая матрицаЧасть 4. Формовка.
Работа проходила с использованием листа поликарбоната толщиной 2 мм. Сначала пришлось найти вакуумный насос. Затем лист поликарбоната винтами М3х10 был прикручен к матрице. Между листом поликарбоната и матрицей, в том месте где они контактируют, «на холодную» промазано вакуумной смазкой (очень тонким слоем).
Матрицу с поликарбонатом нагревают до 200градС в термостате в течение 10мин. Потом достают и откачивают из нее воздух. Аналогично выполняется формирование второй фары..
К сожалению формовка, не обошлась без недочетов, наверное, зря пользовались смазкой, так как на готовом стекле остались какие-то пятна. Не понятно, — от смазки или от перегрева. Поэтому полученные стекла пришлось рпосто отполировать.В дальнейшем автор предпримет еще одну попытку, с более низкой температурой термостата.
Также зря было сделано целых три точки отсоса воздуха из матрицы. Оказалось очень проблематично успеть быстро подсоединить 3 патрубка вакуумного насоса, пока еще не остыло стекло. Так что матрицу тоже неплохо бы доработать на один патрубок.
Готовое изделиеПрикрученный к матрице поликарбонатВакуумный насосВот фото собственно готовых фар:
Готовое стекло в фареГотовое стекло в фареГотовое стекло в фареВся информация про выполненную работу найдена на опель-клубе, вот здесь.